YORK® Absorption Chiller and Heat Pump Technology
Increased Reliability and Efficiency Through Innovation.
Growing environmental and energy conservation considerations require innovative chiller plant designs – something only a global leader in chiller technology can deliver. As an industry leader with decades of experience in the category, YORK® absorption chillers and heat pumps offer the most advanced, most diverse portfolio suitable for a variety of global applications.
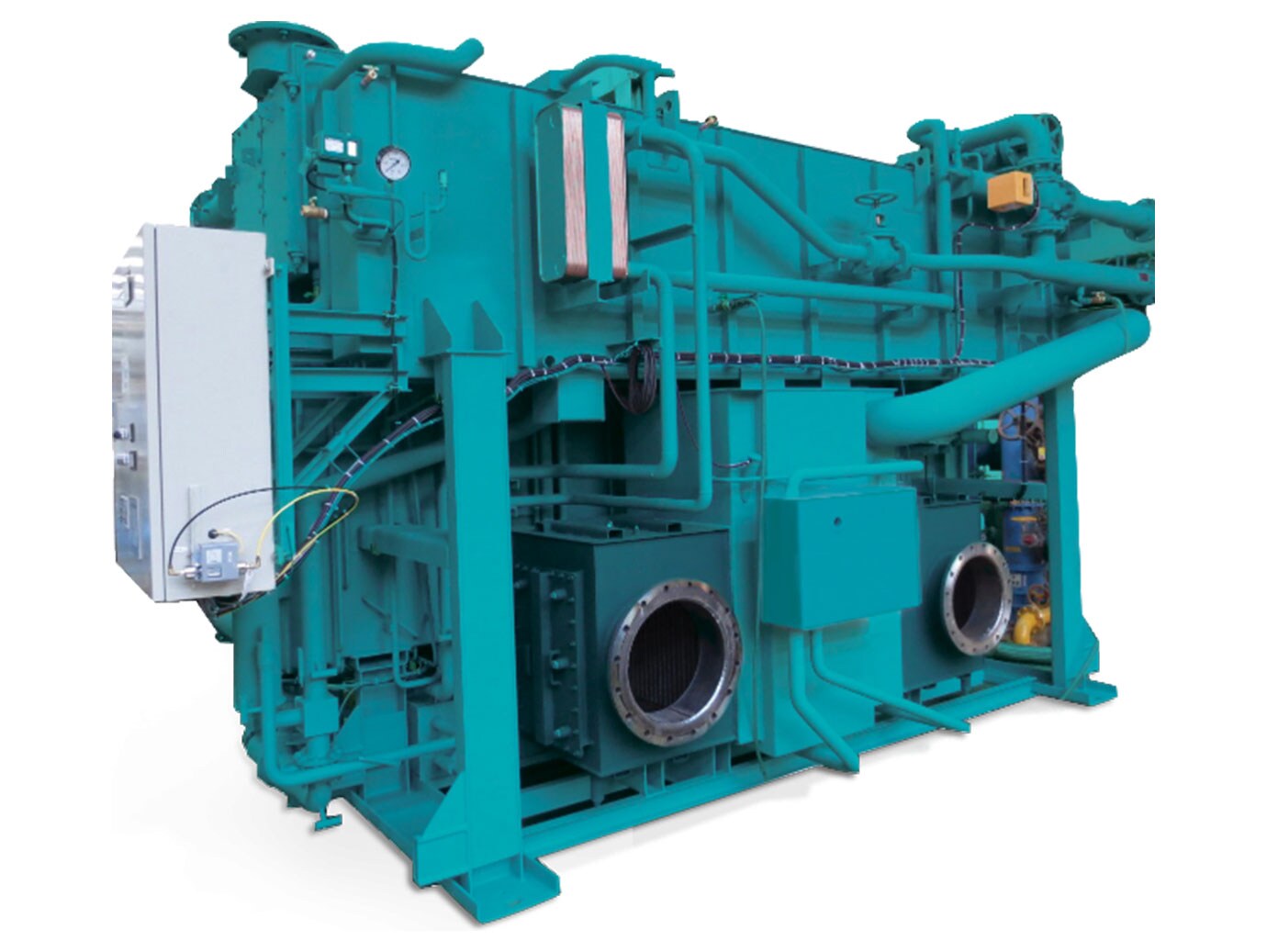
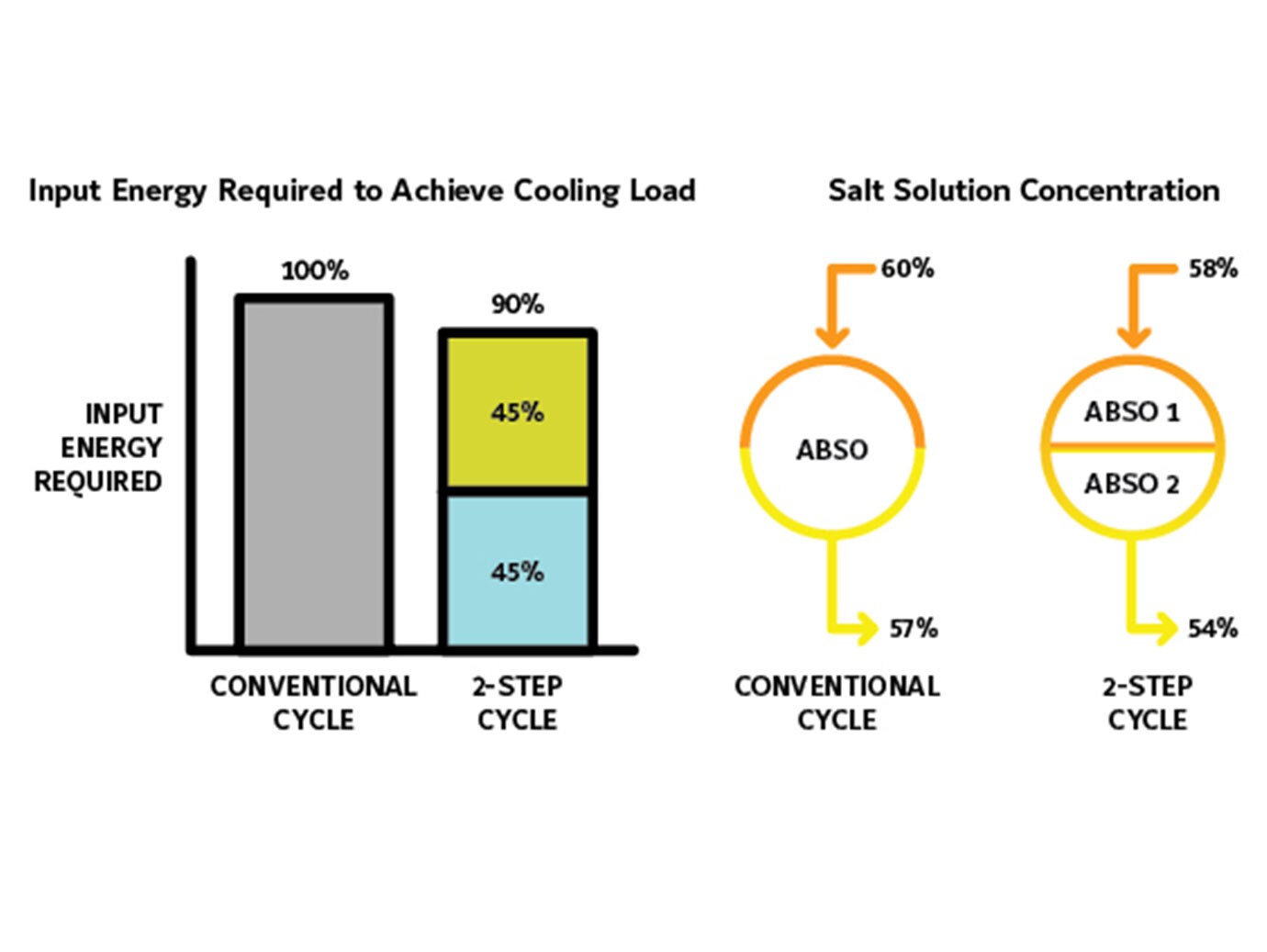
The YORK® Difference.
2-step evaporator and absorber design
In the 2-step evaporator-absorber design, the evaporator and absorber are split into lower and upper sections. This creates two different pressure levels, enhancing absorption compared to a conventional cycle. The different pressure levels help divide the cooling load and the absorption process into two parts. The two-part process effectively saves around 10% in energy usage when compared to a traditional, single-step evaporator/absorber design.
As a result, absorption requires lower generator temperatures – which produce less noncondensable gas and less purging frequency. This also means a better vacuum, more reliable operation, reduced risk of crystallization and a longer life for the chiller.
As a result, absorption requires lower generator temperatures – which produce less noncondensable gas and less purging frequency. This also means a better vacuum, more reliable operation, reduced risk of crystallization and a longer life for the chiller.
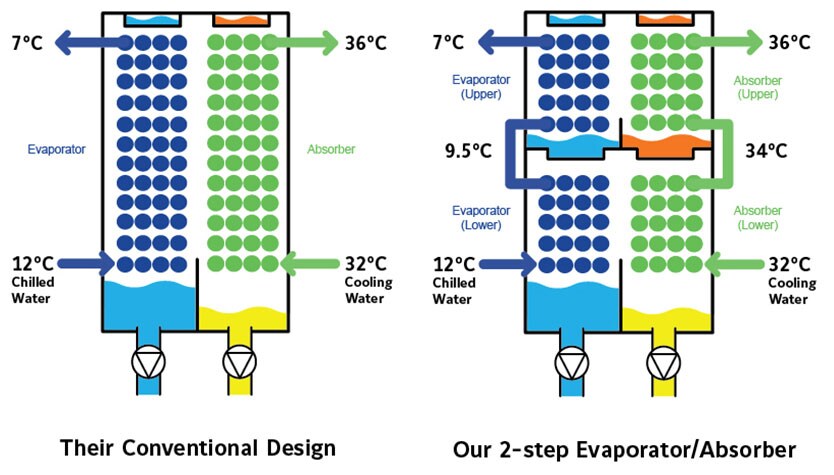
Parallel Flow
Parallel flow divides the LiBr solution flow between the low- and high-temperature generators into two parallel, balanced paths. One goes to the high temperature generator (HTG), while the other goes to the low temperature generator (LTG). The result is safe, more efficient operation at a much lower pressure than conventional, series-flow designs.
When combined with the 2-step evaporator/absorber cycle this design uses a lower LiBr concentration, making it easier to heat in the generator section. Therefore, a relatively lower grade for the driving heat source, providing high COP.
When combined with the 2-step evaporator/absorber cycle this design uses a lower LiBr concentration, making it easier to heat in the generator section. Therefore, a relatively lower grade for the driving heat source, providing high COP.
Combined Parallel Flow and 2-Step Evaporator/Absorber Technology
This combination operates the furthest from the crystallization line (29°C/52.2°F), boosting reliable operations.
See How Other Flow Types Compare
Decades of Experience. A Global Network of Service and Parts.
Absorption cooling and heating technology acquired by Johnson Controls has served the global market since the 1960s. Having been at the forefront of progress and development in chiller technology for decades, some notable technology milestones include:
- Parallel flow cycle, double-effect steam chiller (1972)
- Type-I heat pump (1981)
- Low evaporator leaving temperature minus 5°C (2000)
- 2-step evaporator-absorber technology, highest efficiency (COP 1.5) for direct fired (2001)
- Single-effect double lift with 2-step evaporator and parallel flow cycle (2017)
We continue to invest in technology, providing the most advanced products backed by best-in-class manufacturing and our global service and parts support network. Our ongoing investments have led to advances and services like:
- Superior hermetic integrity: High quality process and rigorous helium leak detection techniques
- Factory functional testing on single-piece shipments: Control-panel and safety device operation to reduce on-site start time
- The largest HVAC service and preventative maintenance organization: Reliable, local service and parts